APQP process的問題,透過圖書和論文來找解法和答案更準確安心。 我們找到下列懶人包和總整理
APQP process的問題,我們搜遍了碩博士論文和台灣出版的書籍,推薦蒲山寫的 ISO/TS 16949體系文件實戰解密 可以從中找到所需的評價。
另外網站What are APQP and PPAP? - Elsmar Cove也說明:APQP is the entire quality planning process from designing a concept through PPAP (see below). This typically includes, but is not limited to, ...
逢甲大學 專案管理碩士在職學位學程 陳昶憲所指導 余國華的 新產品開發流程之內部利害關係人關鍵需求因子探討 - 以半導體A公司為例 (2021),提出APQP process關鍵因素是什麼,來自於新產品開發、內部利害關係人、AHP層級分析法。
而第二篇論文國立高雄科技大學 模具工程系 鄭瑞鴻所指導 沈嘉宏的 車用散熱風扇模具設計與製造最佳化研究 (2021),提出因為有 產品設計、模流分析、田口品質方法、ANN 類神經網路、最佳化設計的重點而找出了 APQP process的解答。
最後網站9145 Advanced Product Quality Planning and ... - IAQG則補充:The 9145 standard was created to define the aviation, space, and defense process requirements for Advanced Product Quality Planning (APQP) and Production ...
ISO/TS 16949體系文件實戰解密
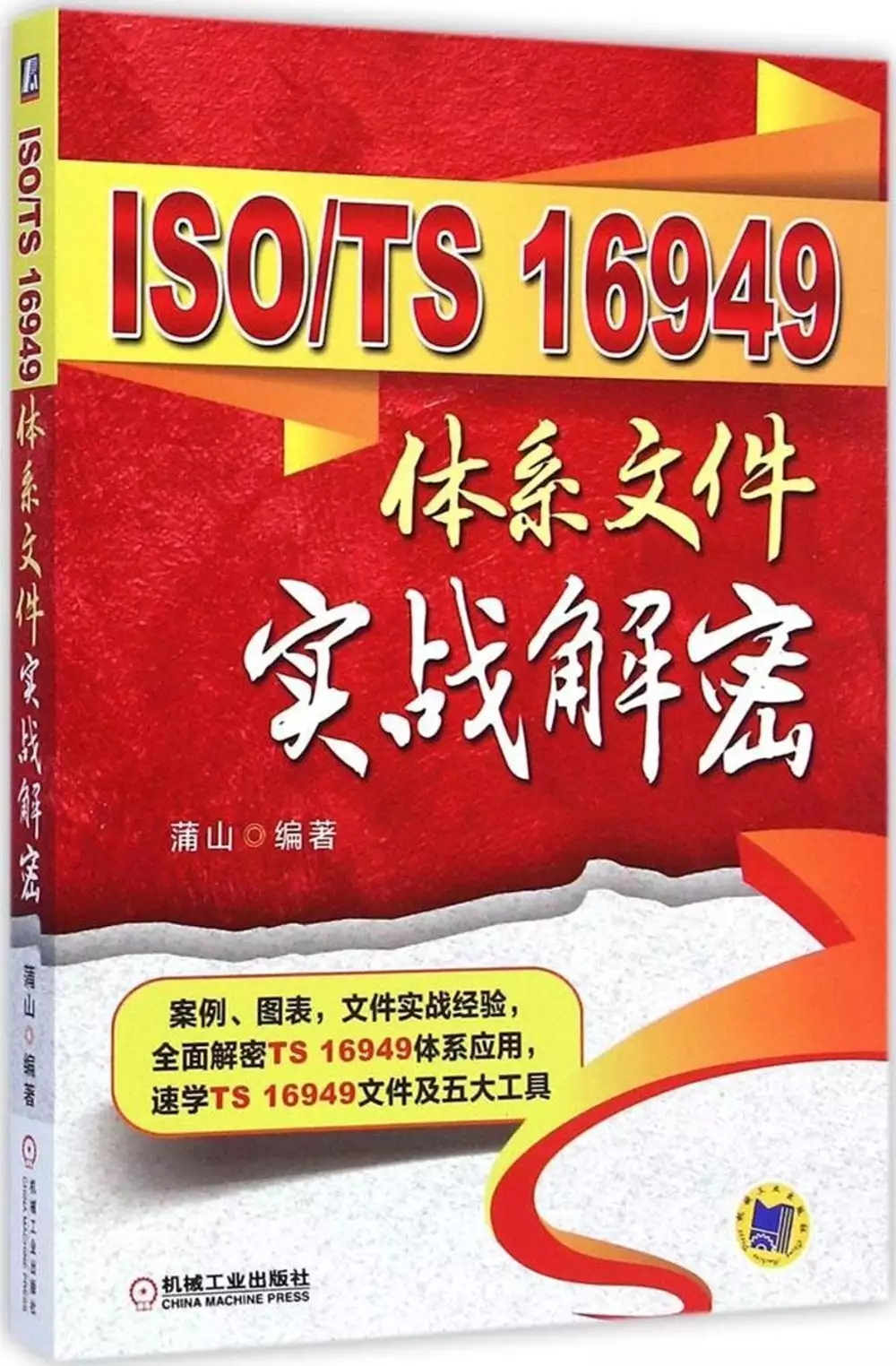
為了解決APQP process 的問題,作者蒲山 這樣論述:
該書共9章。第1章從總體策划出發,概述了質量管理體系文件的實戰應用;第2章對八項質量管理原則作了解讀與應用說明;第3章對相關術語進行了解讀並作了深入比較;第4、5、6、7章分別從質量手冊、程序文件、工作指示、表單與記錄的編寫要求、內容、需注意的「常見病」等方面加以闡述,同時各章給出了豐富、詳盡、具體且能「拿來」即用的案例;第8章描述了體系推行與認證的流程和思路;第9章作為質量管理體系應用升華部分,概論了產品創新與設計方法(PIDM)的結構化流程、內容,PIDM模型及其特點。本書可供那些了解ISO9001,而又想提升、借鑒ISO/TS16949技術規范及其精髓的組織或個人參考
,更可供那些想直接建立或優化ISO/TS16949質量管理體系的組織參考,包括組織中的領導者,以及產品研發、項目、質量、生產、技術、工程、企管等方面的管理和工程技術人員,培訓與咨詢、審核人員,大專院校、科研院所人員參考。蒲山,1995年畢業於西南民族大學電子技術及微機應用專業;曾任職中歐(Philips)、愛默生(Emerson)、聯想、康佳,現任深圳智慧之光創新管理首席顧問;有多家世界500強企業工作經歷,並有15年以上汽車零部件行業以及與大眾、通用、戴姆勒—克萊斯勒等車廠配套經驗。擅長產品創新與研發系統建立,ISO/TS16949及其配套五大工具的應用,以及質量、項目、可靠性、產品等管理,
且能有效就上述相關內容作實質性改進和整合。還是「產品創新與設計方法(PIDM)」的創立和研究者。
新產品開發流程之內部利害關係人關鍵需求因子探討 - 以半導體A公司為例
為了解決APQP process 的問題,作者余國華 這樣論述:
新產品開發專案中的內部利害關係人,是在一個組織中會影響專案目標或被專案影響的團體或個人,而這些利害關係人都有可能會影響到專案成敗,因此利害關係人的規劃、溝通、參與管理極為重要。但實務上在新產品開發完成後執行技術移轉至量產團隊時,常常發生移轉不順等問題,若能從內部利害關係人中找出新產品開發流程中影響技術移轉的關鍵因子,將能有效縮短新產品導入量產的時間週期。有鑑於此,本研究首先藉由新產品開發的文獻探討與個案的開發流程分析來建立AHP層級架構,共建構出四大構面與十六項開發需求因子並據此來設計問卷,再加以深度訪談來深入了解受訪者的問題所在,最後經由AHP層級分析法的分析找出關鍵構面與關鍵因子的重要度
排序,並據以提出新產品開發流程之改善對策。 本研究發現產品開發團隊與量產團隊對新產品開發流程的開發構面之重要度認知有顯著的不同,產品開發團隊較重視風險管理與其階層下的風險回饋與系統修正;而量產團隊比較重視量產能力與其階層下的產品良率。透過訪談得知是因為彼此的立場與觀點不同造成差異,但對於開發流程延伸至量產階段來說這些構面都同等重要,而量產能力一般較容易被開發團隊所忽略。本研究建議如下:1.新產品開發團隊應強化量產能力構面下的電腦整合製造系統的建立與及早針對設備MTBA(技術員平均故障排除週期)進行改善。2.開發過程中持續回饋與修正是非常重要的,並藉不斷的持續改善來降低新產品開發的
風險,並將開發後的開發經驗存入資料庫。3.產品與製程相關開發經驗的資料庫建立與運用,將可有效降低未來新產品開發之初始風險判斷,並可立即採取有效對策來有降低開發時程與節省開發資源。4.另外若量產團隊能提早涉入新產品開發,勢必對新產品加快導入量產有極大助益。
車用散熱風扇模具設計與製造最佳化研究
為了解決APQP process 的問題,作者沈嘉宏 這樣論述:
謝誌 iii目錄 iv圖目錄 vii表目錄 ix第一章、緒論 1研究背景 1研究動機與目的 2第二章、文獻探討 32.1 車用散熱風扇品質系統要求 32.1.1 ISO/TS 16949品質管理系統 32.1.2 TS16949五大核心應用工具 42.1.3 TS16949新產品開發流程 52.2 塑膠模具設計製造 72.2.1塑膠產品射出原理 72.2.2 DFMA設計方法 82.2.3 CAE模流分析 92.3穩健設計與製造最優化 102.3.1 六標準差 (Six Sigma) 102.3.2 QFD品質機能展開 112.3.3 田口品質工程分
析方法 (Taguchi Method) 122.3.3.1 田口方法實驗步驟 122.3.3.2 田口直交表設計 122.3.3.3 田口品質特性與訊號雜音比 (S/N Ratio) 132.3.3 ANN類神經網路 14第三章、研究方法 153.1 研究方法與架構 153.2 預期成果 17第四章、車用散熱風扇設計分析 184.1 以QFD方法做為車用散熱風扇的設計輸入 184.2 車用散熱風扇設計參數與流程 214.2.1車用散熱風扇設計參數 234.2.2車用散熱風扇扇葉之立體模型建構流程 244.3 車用散熱風扇模具設計流程與要點 254.3.1
模具標準化 254.3.2 車用散熱風扇模具設計方法 254.3.3 車用散熱風扇模具設計結果 304.4 以Moldflow模擬分析車用散熱風扇初步結果 324.4.1 產品充填分析 324.4.2 射出壓力分析 334.4.3 壓力損失分析 334.4.4 結合線及強度評估 344.4.5 翹曲分析 344.4.6 以Moldflow模擬分析驗證結果 354.5 以實驗設計方法優化車用散熱風扇分析結果 364.5.1 因子與水準選定 364.5.2 田口方法直交表配置 374.5.3 田口方法實驗結果與分析 394.5.4 田口方法最佳化結果 424.5.4.
1 重量最佳化結果 424.5.4.2 時間最佳化結果 444.5.4.3 品質最佳化結果 47第五章、以模具驗證車用散熱風扇設計與分析 495.1 車用散熱風扇成型材料選用 495.2 塑膠成型射出機選用 515.3 車用散熱風扇模具加工製造 555.3.1車用散熱風扇模仁加工 565.3.2車用散熱風扇三版式模座 585.4 實際產品與實驗結果驗證 595.4.1 車用散熱風扇產品第一次試模 595.4.2 車用散熱風扇產品正式試模 635.4.3 最佳化射出驗證 655.5 應用ANN人工神經網路預測品質 685.5.1 ANN人工神經網路 輸入層 (
Input layer) 685.5.2 ANN人工神經網路 隱藏層 (Hidden layer) 695.5.3 ANN人工神經網路 輸出層 (Output layer) 705.5.4 ANN人工神經網路結果 71第六章、結果與建議 746.1 結論 746.2 後續建議 77參考文獻 78
想知道APQP process更多一定要看下面主題
APQP process的網路口碑排行榜
-
#1.What is APQP? - Plexus International
What is Advanced Product Quality Planning (APQP)? ... The APQP process serves as a guide in the product development process, and a standard ... 於 plexusintl.com -
#2.Advanced Product Quality Planning (APQP) Definition
Advanced Product Quality Planning (APQP) is a methodology that brings together a series of techniques and procedures required to establish a quality plan, ... 於 www.isixsigma.com -
#3.What are APQP and PPAP? - Elsmar Cove
APQP is the entire quality planning process from designing a concept through PPAP (see below). This typically includes, but is not limited to, ... 於 elsmar.com -
#4.9145 Advanced Product Quality Planning and ... - IAQG
The 9145 standard was created to define the aviation, space, and defense process requirements for Advanced Product Quality Planning (APQP) and Production ... 於 iaqg.org -
#5.What is APQP? - Böhme & Weihs
APQP is a highly structured project management tool based on the fact that the quality of a product is essentially the result of planning and ... 於 www.boehme-weihs.de -
#6.APQP Management Software and Processes | Syncronology
Done badly, it becomes a heavy burden on your time and effectiveness. Singlepoint APQP Manager bridges the communications gap between teams and processes and ... 於 www.syncronology.com -
#7.Digitize Your Product Quality Planning Process for ...
Operationalize Quality with APQP. As an automotive manufacturing supplier, you have to produce documents that comply with your customer requirements. But does ... 於 www.plex.com -
#8.IATF 16949: Establish Advanced Product Quality Planning ...
APQP will minimize the risks inherent to the production processes, such as process failures, and effective risk management brings better quality ... 於 advisera.com -
#9.Product Development Process (PDP) / APQP Suppliers
Product Development Process (PDP) / APQP Suppliers. Customer project gates. 18. Packaging and Logistics Concept. 17. Process instructions. 於 www.schaeffler.de -
#10.APQP - Ensuring a Successful Product Launch | IndustryStar
This issue ultimately led to the birth of the APQP process. Advanced Product Quality Planning. APQP is a structured framework that supports ... 於 www.industrystar.com -
#11.APQP & PPAP Software | Advanced Product Quality Planning
Electronically define, schedule, and track APQP and PPAP deliverables with electronic review and signature process. 於 www.net-inspect.com -
#12.APQP - Lean Manufacturing and Six Sigma Definitions
The APQP process is cross-functional, so teams can work together to design a product that meets the customer requirements and is manufacturable with minimal ... 於 www.leansixsigmadefinition.com -
#13.What are APQP activities in product development - Learnmytool
The production part approval process (PPAP) is an output of APQP processes and techniques. PPAP highlights the evidence established through ... 於 www.learnmytool.com -
#14.High QA Blog: 5 Steps to Simplify Your APQP & PPAP Process
APQP is a structured approach to product and process design that facilitates transparent communication and feedback throughout manufacturing ... 於 www.highqa.com -
#15.APQP Explained: 2021 Guide - Capvidia
Phase 1: Planning · Phase 2: Product Design and Development · Phase 3: Process Design and Development · Phase 4: Product and ... 於 www.capvidia.com -
#16.Advanced Product Quality Planning | Siemens Software
Optimized product quality planning with APQP supports a structured method of defining and initiating the necessary process steps. This systematic approach ... 於 www.plm.automation.siemens.com -
#17.What's the Difference Between APQP and PPAP?
5 Phases of APQP · Plan and Define Program · Product Design and Development Verification · Process Design and Development Verification · Product and ... 於 www.inspectionxpert.com -
#18.(APQP) Advanced Product Quality Planning - AIAG
Control Plans summarize the identified process and product parameters required to maintain product conformity. These tools are applicable throughout the supply ... 於 www.aiag.org -
#19.APQP介绍- MBA智库文档
先期產品品質規劃與管制計劃(APQP) APQP A (Advanced) 先期的 P (Product) 產品 Q ... doing and relate it to the APQP process described by the reference manual. 於 doc.mbalib.com -
#20.Advanced Product Quality Planning (APQP) - The Sempre ...
High QA APQP software gives you the framework to control processes and procedures throughout product development. It covers the following phases:. 於 www.thesempregroup.com -
#21.Documentation for PM/APQP/PPAP Processes | Study.com
PPAP, Production Part Approval Process, is part of the bigger process of Advanced Product Quality Planning (APQP). This lesson explores the... 於 study.com -
#22.Flow Chart - Part of the APQP Process - Autobolt Blog - The ...
APQP involves bringing all the affected parties together to formalize the processes that supplies Customer their product. We at Auto Bolt utilize APQP. 於 blog.autoboltusa.com -
#23.Présentation PowerPoint - Camso
Advanced Product Quality Planning (APQP) and Production Part Approval Process (PPAP) Training Material. Nordin Mimouni – Supplier Quality Manager 於 camso.co -
#24.What Is the APQP? (Advanced Product Quality Planning ...
The APQP, or Advanced Product Quality Planning, is a proven approach for developing a new product to be made in high volume and under strict ... 於 qualityinspection.org -
#25.APQP - Advanced Product Quality Planning | Babtec
With APQP, manage centrally and with regard to the project status all the project-related data and documents that have been collected, for example, as part of ... 於 www.babtec.de -
#26.Advanced Product Quality Planning - TR Fastenings
To ensure all quality requirements are met for the parts we supply, TR adopts an APQP process for all automotive customers which can be utilised on request ... 於 www.trfastenings.com -
#27.Implement an Effective APQP Process with Rocket TRUcentrix
B2B Supply Chain Integration meets your APQP needs with TRUcentrix, a comprehensive collaboration and process automation solution with a built in APQP task ... 於 www.rocketsoftware.com -
#28.What is APQP? - IATF 16949 Store
APQP stands for Advanced Product Quality Planning. It is a disciplined process for suppliers to ensure they are capable of designing product and/or ... 於 16949store.com -
#29.5 Key Considerations for Successfully Implementing ...
... of the APQP process at companies of all sizes across industries. ... for Successfully Implementing Advanced Product Quality Planning (APQP). Speaker. 於 www.complianceonline.com -
#30.APQP Software from DELMIAworks - SOLIDWORKS
A centralized, integrated solution to perform all the phases in the APQP Process. The APQP module in DELMIAWorks (formerly IQMS) facilitates compliance to ... 於 www.solidworks.com -
#31.Advanced Product Quality Planning - Medical Device APQP
It spans design and prototyping steps, facility and equipment requirements, the full manufacturing process, production control, production training and ramp-up. 於 empowermedicaldevices.com -
#32.Advanced Product Quality Planning - NPD Solutions
The APQP process is described in AIAG manual 810-358-3003. Its purpose is “to produce a product quality plan which will support development of a product or ... 於 www.npd-solutions.com -
#33.Advanced Product Quality Planning (APQP)
•Packaging Standards. & Specifications. •Product/Process. Quality System. Review (Technical. Review). •Process Flow. Diagram. •Floor Plan Layout. 於 osn.oshkoshcorp.com -
#34.Advanced Product Quality Planning (APQP) & Production Part ...
... (APQP) & Production Part Approval Process (PPAP) Training Course. ... Planning (APQP) to ensure that their products and production processes meet the ... 於 learning.sgs.com -
#35.How Layered Process Audits Support the APQP Process
However, manufacturers can use LPAs to verify a wide range of quality processes, including advanced product quality planning (APQP). To learn more, we spoke ... 於 www.ease.io -
#36.(PDF) Introduction to APQP | brito v - Academia.edu
3 Training Scope – Need to accomplish Introduces the concept of Advanced Product Quality Planning (APQP) process. Defines a typical program management ... 於 www.academia.edu -
#37.Advanced Product Quality Planning C1886 - SAE International
The Automotive Industry Action Group (AIAG) identifies and documents the process for APQP and the related manual is the standard for APQP. This course provides ... 於 www.sae.org -
#38.What is APQP? - AS9100 Store
APQP stands for Advanced Product Quality Planning. It is a disciplined process for suppliers to ensure they are capable of designing product and/or ... 於 as9100store.com -
#39.A simple method to learn about APQP | Procedure of APQP
To define the procedure for APQP (Advanced Product Quality Planning) activities including various stages of development of Prototype/Product sample, ... 於 learnqctools.in -
#40.Apqp ppt - SlideShare
APQP is a process, not. Summary: The 5 Phases of APQP 1.Plan and Define the Program 1. APQP Acronyms APQP – Advance Product Quality Planning D/P-FMEA – Design/. 於 www.slideshare.net -
#41.APQP: Production and Quality Planning - Global Plastics
At Global Plastics, we put every product or part we handle through a rigorous APQP (advanced product quality planning) process to ensure optimal results. 於 www.global-plastics.com -
#42.What is Advanced Product Quality Planning (APQP)?
APQP is a structured process with standardized methods such as Design & Process FMEA, the PPAP process, as well as various documentation and commercial ... 於 www.germanedge.com -
#43.Planning & Realization of Design Processes: Part 1 - Lorit ...
Let's start with APQP. APQP is a product-related quality planning process that supports the development of products and processes. APQP serves as a guide for ... 於 lorit-consultancy.com -
#44.Advanced Product Quality Planning (APQP) - Plianced Inc.
APQP facilitates communication between the supply chain and the organization / customer. Requirements that translate into more detailed ... 於 www.plianced.com -
#45.Advanced product quality planning - Wikipedia
Advanced product quality planning (APQP) is a framework of procedures and techniques used to develop products in industry, particularly in the automotive ... 於 en.wikipedia.org -
#46.APQP - Advanced Product Quality Planning & Control Plan
APQP (Advanced Product Quality Planning) is a cross-industry quality approach which was originally developed by the US automotive industry. 於 www.en-standard.eu -
#47.Advanced Product Quality Planning (APQP) 3 Keys to Long ...
Many manufacturers try posting the process chart on a board somewhere in a hallway or meeting room to make the APQP process definition more ... 於 m.engineeringnews.co.za -
#48.Advanced Product Quality Planning
APQP techniques into their design/manufacturing processes. In the past, Chrysler, Ford, and General Motors each had their own guidelines and formats. 於 cdn.website-editor.net -
#49.Stages in a Robust APQP Process - Enventure
The APQP process consists of five stages: · Planning · Product Design and Development · Process Design and Development · Product and Process ... 於 www.enventure.com -
#50.You Need to Know About APQP: Definition, Steps and Benefits
5 Phases of the Advanced Product Quality Planning (APQP) Process · 1. Define and Plan the Program · 2. Designing and Developing the Product · 3. Aligning ... 於 tallyfy.com -
#51.Q1A Advanced Product Quality Plan (APQP) & Production Part ...
An output of APQP is the Production Part Approval Process (PPAP). PPAP provides evidence that all Buyer engineering design record and ... 於 www.lockheedmartin.com -
#52.Advanced Quality Planning (APQP): planning tool - DataScope
APQP is a structured process to define the main characteristics for compliance with ... 於 datascope.io -
#53.Advanced Product Quality Planning (APQP) - Blackhawk ...
We align our internal processes with customer-specified APQP process for both new and existing parts to continually drive efficiencies. 於 www.blackhawkengineering.com -
#54.APQP (Advanced Product Quality Planning) - Creative Safety ...
Phase 3: Process Design and Development: The third phase is all about planning the manufacturing process for producing the product. Manufacturing techniques ... 於 www.creativesafetysupply.com -
#55.APQP - ASQ Automotive Division
Advanced Product Quality Planning (APQP) is structured process that includes critical tasks from concept approval through production. 於 www.asq-auto.org -
#56.Advanced Product-Quality Planning (APQP) - Ingenics AG
Continuous quality control with APQP makes it possible to minimize risks in the product development process. We help you to use APQP. 於 www.ingenics.com -
#57.Advanced Product Quality Planning (APQP) - Control Plan
Control plans, whether being used for APQP or not, are an excellent tool for monitoring product and process key characteristics and critical ... 於 www.nqa.com -
#58.Training on Advance Product Quality Planning (APQP ...
VIRTUAL CLASSES SCHEDULE. 8th May 2020 - Training on Advance Product Quality Planning (APQP) & Production Part Approval Process (PPAP) | Duration: 1 Day 於 www.tuvsud.com -
#59.APQP (Advance Product Quality Planning)
How to Implement APQP process? Fundamentals of APQP; Phases in APQP process. Phase #1 – Planning; Phase #2 – Product design & ... 於 qualityengineerstuff.com -
#60.Plan for Success with the APQP Process - Automotive ...
The Advanced Product Quality Planning Process (APQP) is the process that allows suppliers, designers, manufacturers and customers to communicate ... 於 www.automotiveengineeringhq.com -
#61.Advanced Product Quality Planning |Product Part Approval ...
Advance Product Quality Planning (APQP) and Product Part Approval Process training from TQMI help delegates to design and implement products that meet ... 於 www.tqmi.com -
#62.APQP & PPAP - Smallpeice Enterprises Limited
This course concentrates on the essentials of APQP & PPAP process required to set-up new ... new product designs and corresponding manufacturing processes. 於 www.smallpeice.com -
#63.What is APQP ? APQP Phases | APQP Checklist - Tech ...
APQP – Advanced Product Quality Planning is a structured approach that is used to design and develop the product ... 於 techqualitypedia.com -
#64.APQP (Advanced Product Quality Planning)
APQP process is defined in the APQP manual from AIAG, which is part of a series of documents that AIAG mutually controls and publishes. This ... 於 managementmania.com -
#65.What is APQP? - Pro QC International - Blog
Advanced Product Quality Planning, APQP, exists to ensure suppliers and manufacturers produce products that meet or exceed customer ... 於 proqc.com -
#66.APQP 先期产品质量策划&PPAP生产件批准程序应用能力提高 ...
APQP (Advanced Product Quality Planning) & PPAP(Production Part Approval Process) Application(in Chinese Language)-APQP 先期产品质量策划&PPAP生产件批准程序 ... 於 www.europeanchamber.com.cn -
#67.APQP Process Implementation(C-MEC-AUTNA00-APQ-ENL1)
Attend this online training on APQP to gain an overview of overall APQP Process Implementation in Automotive and Discrete Manufacturing domain. 於 edstelearning.com -
#68.GM Global APQP - WordPress.com
develop a GM Common APQP process. Prior to this, each General Motors Supplier Quality organization facilitated the implementation of the APQP process using ... 於 ingenieriadeautomocion.files.wordpress.com -
#69.APQP Checklist | Free PDF Download | SafetyCulture
APQP has 5 Phases: Plan and Define Program; Product Design and Development Verification; Process Design and Development Verification; Product & ... 於 safetyculture.com -
#70.SoftExpert APQP-PPAP - Terzion DX
It serves as a guide in the product development process, while also standardizing the methods of sharing results between suppliers and manufacturers. 於 processera.com -
#71.What is APQP? - RGBSI Blog
The goal of advanced product quality planning (APQP) is to establish new products and processes that are successful in meeting customer requirements. 於 blog.rgbsi.com -
#72.Advanced Product Quality Planning - An Introduction - We Are ...
What are the five phases of APQP? · Phase 1 – Product Planning and Quality Program Definition · Phase 2 – Product Design and Development · Phase 3 – Process Design ... 於 weareatlas.com -
#73.Advanced Product Quality Planning (APQP) Training - Industry ...
Course overview. Advanced Product Quality Planning, or APQP, is a method for new product or process introduction or the introduction of changes ... 於 industryforum.co.uk -
#74.APQP mit SAP QM und SAP PPM - EN - DHC Consulting
APQP WITH SAP QM. The Advanced Product Quality Management (APQP) project management method is deployed in product development processes, where it aims to ... 於 www.dhc-consulting.com -
#75.How APQP Plays a Critical Role in a Digital Thread - iBASEt
What makes APQP so important is that it provides a framework for focusing on product quality early in the design process and includes the ... 於 www.ibaset.com -
#76.Training Program on Advance Product Quality Planning ...
Training Program on Advance Product Quality Planning (APQP) & Production Part Approval Process (PPAP). Home · Services · TUV India Training Academy ... 於 www.tuv-nord.com -
#77.Source-to-APQP - SupplyOn
Source-to-APQP: Thanks to web-based SupplyOn solutions, you can standardize the mapping of all source-to-contract processes throughout your company. 於 www.supplyon.com -
#78.APQP: A Strong Approach to NPI (New Product Introduction)
The Advanced Product Quality Planning (APQP) process is a structured framework aimed at developing and introducing products that are up to customers' ... 於 www.cmc-consultants.com -
#79.APQP / PPAP - New Product Development - CT Educational ...
ADVANCED PRODUCT QUALITY PLANNING & PRODUCTION PART APPROVAL PROCESS. Two Day Work Shop Presented By CTRI ( CT Research Institute). Research and Training wing ... 於 cteducational.org -
#80.What Is APQP? | Ideagen
Basically, APQP deals with the entirety of the process - from receiving a business enquiry all the way to the finished product. Putting APQP ... 於 www.ideagen.com -
#81.AQuA Pro APQP Software | FMEA | Control Plan - Omnex ...
This APQP process defines and documents the product development process: from design, to manufacturing, to continuous improvement, thus helping organizations ... 於 www.omnexsystems.com -
#82.apqp process - Spanish translation – Linguee
Many translated example sentences containing "apqp process" – Spanish-English dictionary and search engine for Spanish translations. 於 www.linguee.com -
#83.Advanced Product Quality Planning (APQP) - Stunell ...
Why you need APQP. Developing new products and improving production processes are essential if you want to establish or maintain a competitive ... 於 www.stunell.com -
#84.Future of APQP and PPAP in Doubt | Quality Magazine
... Advanced Product Quality Planning (APQP) and Production Parts Approval Process (PPAP) and their applications--which were born out of ... 於 www.qualitymag.com -
#85.Designing Cast Products: Starting the APQP Process with the ...
Learn how the best casting foundries use the APQP process to ask the right questions during product development, resulting in saved time, ... 於 blog.eaglegroupmanufacturers.com -
#86.APQP Training Program - Reliatrain
APQP is a structured method that defines and establishes steps necessary to ensure supplier parts meet the customer requirements and expectations. APQP supports ... 於 reliatrain.com -
#87.APQP+PPAP for suppliers in the aviation industry - AeroImpulse
Product and process risks in the phase after series release, whether in design, manufacturing technology or the supply chain, are thus minimized. p. The history ... 於 www.aeroimpulse.de -
#88.Advanced Product Quality Planning (APQP)
The abbreviation APQP stands for Advanced Product Quality Planning, which is a widely used systematic method to plan quality up front, ... 於 www.qmindset.com -
#89.Advanced Product Quality Planning (APQP) - Omnex
Advanced Product Quality Planning is a structured approach used in the automotive sector to ensure that new products and processes meet customer expectations. 於 www.omnex.com -
#90.(PDF) Process of Quality Planning by the Method APQP
advanced APQP product quality planning method. Keywords- process, quality, planning, management, method. I. INTRODUCTION. At ... 於 www.researchgate.net -
#91.The APQP Process of Advanced Product Quality Planning
Advanced Product Quality Planning (or APQP) is a framework of procedures and techniques used to develop products in industry, particularly the automotive ... 於 www.ejbasler.com -
#92.Advanced Product Quality Planning | SoftExpert APQP-PPAP
SoftExpert APQP-PPAP. A system for planning and controlling the development of your company's products and processes. 於 www.softexpert.com -
#93.What is APQP? - QualityTrainingPortal
Advanced Product Quality Planning, or APQP for short, creates a roadmap for developing new products complete with time-based milestones and decision points ... 於 qualitytrainingportal.com -
#94.Advanced Product Quality Planning / APQP - SatiStar ...
APQP is a defined process for product development that provides a common path (between supplier and customer) and synchronization of these development ... 於 satistar.com -
#95.Advanced Product Quality Planning (APQP)
APQP is a structured approach to product and process design. This framework is a standardized set of quality requirements that enable suppliers to design a ... 於 quality-one.com -
#96.What it is APQP | Adaptive BMS
APQP is an excellent project quality tool for both manufacturers and service providers. The APQP process is easily adaptable to almost any type of application ... 於 www.adaptivebms.com