防水防塵測試的問題,我們搜遍了碩博士論文和台灣出版的書籍,推薦陳旺儀,李文進寫的 智慧安全帽商品化功能確認及推廣應用研究 ILOSH110-S314 和王芳夏軍的 電動汽車動力電池系統設計與制造技術都 可以從中找到所需的評價。
另外網站什麼是IP68?簡單看懂防水防塵-國際防護等級認證-技術資料也說明:日常生活中常常會看到各種產品標榜著防水、防塵、IP68等等各種強調產品 ... 要注意的是通過測試的防水產品可以防水但不防肥皂水、海水等特殊液體,每 ...
這兩本書分別來自勞動部勞動及職業安全衛生研究所 和科學所出版 。
國立勤益科技大學 工業工程與管理系 陳水湶所指導 潘書育的 電動式驅動器品質性能改善 (2019),提出防水防塵測試關鍵因素是什麼,來自於閥體、電動驅動器、六標準差、品質機能展開。
而第二篇論文國立彰化師範大學 電機工程學系 陳良瑞所指導 李明聰的 鋰電池系統安全標準與高電壓絕緣防護探討 (2019),提出因為有 鋰電池、安全檢測標準、絕緣阻抗的重點而找出了 防水防塵測試的解答。
最後網站防水測試則補充:金屬中心檢測驗證網www.quality.org.tw/waterproof.aspx 防塵防水IP等級: IP等級可分防塵、防水兩部分,其中防塵共分0~6 七個等級,防水共分0~8 九個等級.
智慧安全帽商品化功能確認及推廣應用研究 ILOSH110-S314

為了解決防水防塵測試 的問題,作者陳旺儀,李文進 這樣論述:
為提升產業安全帽使用上之方便性及安全性,針對勞工於局限空間等特殊作業場所之需求,本所去(109)年已完成照明、攝影、通訊、後台資訊監控及物聯網等新技術之功能整合可行性評估及雛型製作。 本年度延續去年研究成果,為使本商品雛型符合實務上及商品化之需求,召開專家座談會,確認本智慧安全帽商品的最後規格、功能及型式,再據以設計調整及雛型再製作,並強化後端資訊接收之系統功能及顯示介面,開發製作測試樣品所需之模具,模具經測試、修改及樣品之製作,帽殼結構體完成標檢局衝擊強度等測試,符合規範要求,本開發成果並獲中華民國發明專利。 本研究完成產業用智慧安全帽140頂及46件監控器之樣品製作
,帽體含電池總重約730公克,具IP54防水防塵性及藍牙連結功能可擴大應用領域。實用上除照明、攝影及通訊等功能外,後端管理人員透過監控器可了解現場作業環境及勞工活動的資料,有效掌握勞工作業安全。
防水防塵測試進入發燒排行的影片
Cc by choyce.tw
電動式驅動器品質性能改善
為了解決防水防塵測試 的問題,作者潘書育 這樣論述:
閥體是一種控制液體或氣體流動方向及流量的機構裝置,較小的閥體如我們日常常見的水龍頭,而較大的閥體則像是水庫閘刀閥以及冷卻系統管路源頭的閥體...等。隨著工業的發展與進步,自動控制閥體的設備也逐漸成為市場競爭的一環,從早期的氣動控制閥體轉為油壓控制,到現今較熱門的電動驅動器控制,電動驅動器能有效的控制閥門做動,且能精準的控制每個時間點管內液體或氣體的流向及流量。隨著市場需求提升及競爭下,有效的開發出客戶所需產品及降低生產成本,是各企業在市場上生存最重要的一環。因此本文採用六標準差DMADV開發手法並導入品質機能展開QFD,在客戶需求下開發出具市場競爭力的成本以及產品功性能能符合客戶需求的產品。
本研究以控制閥之電動式驅動器為研究主題,使用品質機能展開QFD收集客戶及市場的需求並以六標準差DMADV分析現有產品無法滿足客戶的地方,再由設計階段設計出能提升產品功能性之零組件,並且降低零組件的製造成本確保改良後新產品的售價能滿足客戶及市場的需求,最後在確認階段對改良後新機種進行一系列的功能性及壽命測試,確保產品品質能符合客戶及市場的需求。本研究最終開發出的新機種在市場上已有客戶開始下單購買且陸續有許多客戶購買樣品回廠測試中,這代表著導入正確的開發手法並結合收集市場及客戶需求才能有效的開發出符合市場需求的產品,且達到客戶滿意企業永續經營的目標。
電動汽車動力電池系統設計與制造技術
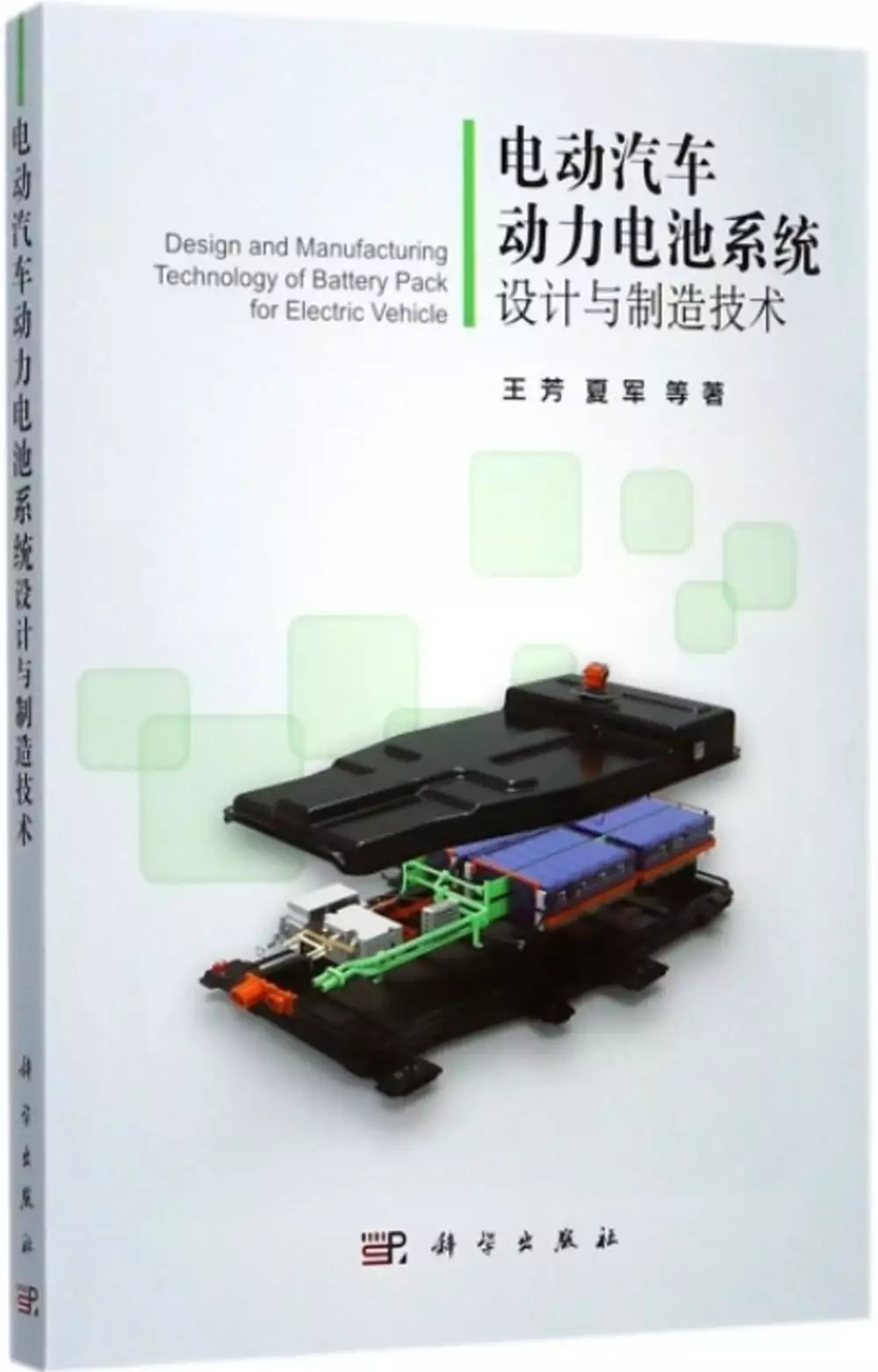
為了解決防水防塵測試 的問題,作者王芳夏軍 這樣論述:
本書內容立足於中國電動汽車產業的實際情況,從多個角度對動力電池系統的設計與製造進行了系統化的梳理和論述,可以用於指導企事業單位的方案論證、產品開發、技術研究、生產製造和售後服務等工作。 全書共8章,包括動力電池系統技術發展綜述、總體方案設計(系統設計)、結構與電連接設計、電池管理系統(BMS)設計、熱管理設計、結構模擬分析、試驗驗證,以及生產製造技術,可以為讀者提供豐富的工程實踐參考。 電動汽車動力電池系統技術發展綜述 1 1.1 電動汽車發展史 2 1.1.1 電動汽車的DIYI個黃金時代 2 1.1.2 電動汽車的第二個黃金時代 2 1.1.3 電動汽
車的第三個黃金時代 4 1.2 電動汽車Pack產品分類 5 1.2.1 動力儲能電池的分類 6 1.2.2 動力電池系統的功能分類 10 1.2.3 動力電池系統在整車的安裝位置 19 1.3 電動汽車Pack的關鍵技術 23 1.3.1 系統集成技術 24 1.3.2 電芯設計及選型 25 1.3.3 結構設計技術 27 1.3.4 電池包電子電氣設計 28 1.3.5 電池包熱設計 29 1.3.6 電池包安全設計 30 1.3.7 電池包模擬分析技術 32 1.3.8 電池包工藝設計 32 1.4 我國電動汽車Pack技術發展趨勢
33 1.4.1 我國新能源汽車的發展階段 33 1.4.2 我國政府制定的2020年關鍵技術指標 34 1.4.3 技術挑戰及發展趨勢 35 參考文獻 38 第2章 動力電池系統總體方案設計 41 2.1 動力電池系統總體方案設計概述 42 2.1.1 動力電池系統總體方案設計流程 42 2.1.2 動力電池系統的總體需求分析 43 2.1.3 動力電池系統的基本性能參數 47 2.1.4 動力電池系統產品參數匹配性分析 48 2.2 單體電池的選型與設計 51 2.2.1 單體電池的選型與設計概述 51 2.2.2 單體電池的選型依據
51 2.2.3 單體電池容量選型設計 52 2.2.4 單體電池選型和容量設計示例 53 2.3 機械結構概念設計 57 2.3.1 機械結構總體設計概述 57 2.3.2 機械結構設計要求 58 2.3.3 電池包在整車上的佈置 62 2.3.4 電池包總體佈置方案設計 67 2.3.5 電池箱體和電池模組概念方案設計 69 2.4 電池管理系統概念設計 71 2.4.1 電池管理系統設計概述 71 2.4.2 電池管理系統基本功能 71 2.4.3 電池管理系統設計要求 72 2.4.4 電池管理系統概念設計方案 76 2.5 高
壓電氣系統設計 77 2.5.1 高壓電氣系統設計概述 77 2.5.2 高壓電氣系統設計要求 78 2.5.3 高壓電氣系統概念設計方案 81 2.6 熱管理系統設計 84 2.6.1 鋰離子動力電池的溫度特性 84 2.6.2 熱管理系統設計概述 85 2.6.3 熱管理系統基本功能 86 2.6.4 熱管理系統設計要求 86 2.6.5 熱管理系統概念設計方案 86 參考文獻 90 第3章 動力電池系統結構與電連接設計 93 3.1 電池系統結構設計概述 94 3.2 模組結構設計 95 3.2.1 需求邊界 95 3.2.2
模組的固定與連接 98 3.2.3 模組電連接設計 103 3.2.4 模組安全設計 107 3.2.5 模組尺寸標準化 108 3.3 電箱結構設計 109 3.3.1 需求邊界 110 3.3.2 整體排布設計 110 3.3.3 詳細設計 112 3.3.4 電連接設計 116 3.3.5 電箱安全設計 119 3.4 高壓箱結構設計 123 3.5 輕量化設計 125 3.5.1 新的成組方式 126 3.5.2 新型材料的應用 128 3.5.3 極限設計 129 3.6 IP防護設計 131 3.6.1 接觸防護 1
31 3.6.2 防水防塵 132 參考文獻 138 第4章 動力電池管理系統(BMS)設計 139 4.1 BMS的功能及其重要性 140 4.1.1 BMS的角色定位 140 4.1.2 BMS的主要功能 141 4.2 BMS的硬體開發要點 146 4.2.1 拓撲結構的選擇 146 4.2.2 電壓、電流、溫度採集電路的設計要點 150 4.2.3 BMS中兩個關鍵硬體模組的設計 154 4.2.4 BMS的抗干擾設計 158 4.2.5 面向提高可靠性的冗餘設計 161 4.3 BMS的軟體發展要點 162 4.3.1 SOC相
關的概念 162 4.3.2 電池荷電狀態(SOC)估算 164 4.3.3 電池健康狀態(SOH)評估 167 4.3.4 SOF的估算 170 4.4 BMS的測試與驗證 172 4.4.1 一些值得討論的問題 172 4.4.2 在產品設計、製造的不同階段對BMS 的驗證 173 4.4.3 用於BMS驗證的電池模擬器 174 參考文獻 177 第5章 動力電池系統熱管理設計 179 5.1 熱管理系統設計概述 180 5.1.1 熱管理系統的“V”模型開發模式 180 5.1.2 模擬分析的應用 182 5.1.3 實驗驗證 189
5.2 冷卻系統設計 190 5.2.1 冷卻方式的選擇 191 5.2.2 自然冷卻系統 191 5.2.3 強制風冷系統 193 5.2.4 液冷系統 197 5.2.5 直冷系統 212 5.3 加熱系統設計 214 5.3.1 設計需求 214 5.3.2 電加熱膜設計 216 5.3.3 PTC加熱設計 218 5.3.4 液熱設計 220 5.4 保溫系統設計 222 5.4.1 保溫設計概述 222 5.4.2 模組保溫設計 222 5.4.3 箱體保溫設計 223 5.5 熱管的應用 224 5.5.1 熱管
簡介 224 5.5.2 熱管在熱管理系統中的應用 225 5.5.3 熱管應用注意事項 225 參考文獻 226 第6章 動力電池系統結構模擬分析 227 6.1 電池系統結構優化 228 6.1.1 結構拓撲優化 228 6.1.2 電池殼體結構形貌優化 230 6.1.3 其他優化方法簡介 231 6.2 動力電池系統結構強度模擬 232 6.2.1 彈性變形體的基本假設 232 6.2.2 應力應變基本概念及關係 232 6.2.3 材料模型 235 6.2.4 衝擊分析 236 6.2.5 擠壓模擬分析 240 6.3 動
力電池系統振動疲勞模擬 242 6.3.1 疲勞理論介紹 242 6.3.2 基於極限拉伸強度的S-N曲線估算 245 6.3.3 結構振動疲勞壽命估算 250 6.3.4 隨機振動案例解析 255 6.4 製造工藝模擬 259 6.4.1 衝壓成型模擬 260 6.4.2 超聲波焊接模擬 262 6.4.3 攪拌摩擦焊接 263 6.4.4 模流分析 269 參考文獻 272 第7章 動力電池系統開發性試驗驗證 275 7.1 電池單體測評 276 7.1.1 出廠參數 277 7.1.2 溫度和倍率充電性能 277 7.1.3 溫
度和倍率放電性能 279 7.1.4 恒功率特性 280 7.1.5 脈衝功率特性 281 7.1.6 能量效率 282 7.1.7 荷電保持能力 283 7.1.8 產熱特性 284 7.1.9 老化特性 285 7.1.10 安全性測試 287 7.2 動力電池系統開發性驗證 289 7.2.1 系統功能 289 7.2.2 系統殼體防護功能 292 7.2.3 電性能 295 7.2.4 可靠性 304 7.2.5 安全性 311 7.2.6 熱管理系統開發性試驗驗證方法 316 7.2.7 EMC開發性試驗驗證方法 317
參考文獻 321 第8章 動力電池系統製造技術概述 323 8.1 概述 324 8.2 模組結構和工藝介紹 324 8.2.1 圓柱電芯模組結構和工藝介紹 325 8.2.2 方形電芯模組結構和工藝介紹 329 8.2.3 軟包電芯模組結構和工藝介紹 331 8.3 關鍵工藝介紹 334 8.3.1 電芯分選 334 8.3.2 電阻焊接 335 8.3.3 鍵合焊接 340 8.3.4 鐳射焊接 343 8.3.5 打膠工藝 346 8.3.6 Pack總裝緊固 348 8.3.7 線束裝配 350 8.3.8 氣密性檢測 3
51 8.4 生產程序控制 352 8.5 下線測試(EOL) 359 8.5.1 下線測試(EOL)作用 359 8.5.2 下線測試(EOL)檢測功能需求分析 359 8.6 模組及Pack 資訊/自動化 363 8.6.1 動力電池模組與Pack產線的自動化 363 8.6.2 動力電池模組與Pcak產線的資訊化 365 8.6.3 動力電池模組與Pack產線的智能化 367 8.6.4 本章小結 370 參考文獻 370 縮略語 371
鋰電池系統安全標準與高電壓絕緣防護探討
為了解決防水防塵測試 的問題,作者李明聰 這樣論述:
隨著國際間綠能政策的推廣,鋰電池作為電動車動力應用,或搭配電力調節系統作為儲能應用的市場逐漸成長,而鋰電池的熱失控行為在組成高電壓電池系統後,對使用區域和人員造成威脅,如何基於電池系統的幾項參數,如開路電壓、電容量、電能量、直流內部阻抗和絕緣阻抗來檢測並判斷其安全性,成為重要的電氣防護考量。本論文首先針對ISO、IEC及UL所制定的鋰電池安全檢測標準進行探討,再進一步的考量溫濕度條件試驗程序,最後以高電壓鋰電池組進行絕緣阻抗量測,並針對結果進行探討。
防水防塵測試的網路口碑排行榜
-
#1.IP防塵防水等級定義 - SKCIC久冠測量儀器
IP等級系統提供了一個以電器設備和包裝的防塵、防水和防碰撞程度來對產品進行分類的 ... 為IPX8 / IPX5,其實「X」即是等於0,證明該產品並沒有任何防塵功能. 防水測試 ... 於 www.skcic.com.tw -
#2.防水防塵IP67或IP68等級代表什麼?IP等級測試方法說明與注意 ...
防水防塵 IP67或IP68等級代表什麼?IP等級測試方法說明. 市面上的電子產品為了差異化,有越來越多的產品強調其具有防水功能,比如說Sony當初強調 ... 於 www.researchmfg.com -
#3.什麼是IP68?簡單看懂防水防塵-國際防護等級認證-技術資料
日常生活中常常會看到各種產品標榜著防水、防塵、IP68等等各種強調產品 ... 要注意的是通過測試的防水產品可以防水但不防肥皂水、海水等特殊液體,每 ... 於 www.x-fan.com -
#4.防水測試
金屬中心檢測驗證網www.quality.org.tw/waterproof.aspx 防塵防水IP等級: IP等級可分防塵、防水兩部分,其中防塵共分0~6 七個等級,防水共分0~8 九個等級. 於 monk11251023.pixnet.net -
#5.【秒懂潮科技】手機的IP68 是什麼意思?教你看懂防水防塵等級
現在不少手機都會標榜具備了IP68 防水防塵能力,到底IP68 這些英文跟數字 ... 著防水能力,而在介紹等級差異之前,各位要先知道這個防水等級的測試 ... 於 online.senao.com.tw -
#6.燈具、家電IP防水防塵等級測試標準與具體流程 - 資訊咖
什麼是防水防塵等級測試?IP是Ingress Protection的縮寫,IP等級是針對電氣設備外殼對異物侵入的防護等級,這個標準在2004年也被採用為美國國家標準。 於 inf.news -
#7.IP 防護等級 - CCTV 監視系列產品
IP 防護等級。砂塵與防水試驗。IP 等級系統提供了一個以電器設備和包裝的防塵、防水和防碰撞程度來對產品進行分類的方法,這個系統得到了多數歐洲國家的認可, ... 於 cctv.blueeyes.tw -
#8.IPX防塵/防水等級怎麼分?IPX7或IP58就真的能防水與潛水嗎?
IPX-2 級別基本與IPX-1 相同,屬於防滴Ⅱ型,與垂直方向成15″範圍內落下的水滴無有害的影響,但是可以通過各個方向上翹15 度的防水測試。 IPX-3 防雨型,60 度角度的潑濺 ... 於 shopee.tw -
#9.IPX5、IP67/IP68 代表什麼? 一次看懂《IP (防水防塵) 等級表》
iPhone 7 與iPhone 7 Plus 皆具備防潑抗水與防塵功能,並且已在受控管的實驗室環境條件下測試,達到IEC 60529 標準的IP67 等級。防潑抗水與防塵功能非 ... 於 dacota.tw -
#10.【詳解】什麼是IP67 等級?手機防水防塵標準一次說明
IP68 防水評級是根據測試環境下的測試結果而定:浸在深達1.5 米的淡水長達30 分鐘。不建議在沙灘或泳池使用。 SONY, Xperia 1 II, IP65/IP68, 我們會將 ... 於 www.techritual.com -
#11.防水防塵等級測試常見問題 - 人人焦點
防水防塵 等級測試常見問題. 2021-02-14 嘉峪檢測網. 醫療器械質量與檢測(medtesting). 實驗室經理人(labmanager). 藥研檢測(drugtest). 於 ppfocus.com -
#12.TEST REPORT - 崴海尼可
防水 保護等級. 測試結果:. 結論. 送測樣品經過測試符合IEC 60529 Edition 2.1: 2001 外殼保護程度試驗--IP67 試驗. 要求及合格判定準則。 於 www.wifi-link.com.tw -
#13.防水防塵實驗室 - 正修電機科技中心
防水防塵 實驗室. 本實驗針對各種電器或機械類外殼等試件之防塵及防水等級分類。其測試目的為:. 防止人體觸及外殼內危險部位之保護; 防止固體異物由外殼進入器具內之 ... 於 csu.badsmaru.com -
#14.【ip防塵測試】防水防塵測試-台灣電子檢驗中心 +1 | 健康跟著走
防水防... 防水防塵測試IPX1, 放置樣品之旋轉台其旋轉速率為1轉/分,水流率:1.0mm/min,測試時間10分鍾。 ... 只要是產品有需要防止固態物(solid objects),如手臂、手指、 ... 於 tag.todohealth.com -
#15.IEC 60529防水防塵測試規範- 哈拉聊天區
防水IP等級測試條件IPX1: (1) 放置外殼之旋轉台其旋轉速率為1轉/分, ... IEC 60529防水防塵測試規範,台灣無線電俱樂部TAIWAN RADIO CLUB ( TRC ) 於 www.radio.club.tw -
#16.其他檢測服務- 衝擊/ 鹽霧/ 變溫/ 震動/ 防水防塵測試 - 詎詮科技 ...
智慧電網(變電站自動控制器) IEC 61850-3 , IEEE1613. UL2849 (電動腳踏車, 全世界第二套). IP68(防水防塵測試). 鹽霧測試. 高低溫衝擊測試. 高空/低壓變溫測試(0 – 80 ... 於 www.prodigy-tech.com.tw -
#17.防水防塵測試 - 易胜博ysb88安卓
防塵防水 IP Code 測試. 針對產品的防塵與防水測試要求,依據測試規... 更多... 共1页1条记录. 新聞快訊 · 澳洲灯具Level 3类别新增2项 · 澳洲墙壁开关认证要求修订 ... 於 hk.bjxfbh.com -
#18.NEMA 250 & IP Rating 防水防塵測試認證 - 歐陸檢驗
NEMA 250 & IP Rating 防水防塵測試認證 · 電器製造商協會(National Electrical Manufacturers Association,簡稱NEMA)一家位於美國華盛頓的技術標準機構 ... 於 www.eurofins.tw -
#19.IPxx防塵防水等級 - Kennyradio - 痞客邦
防水 區分為9個等級(等級0 ~ 等級8)在試驗應用上通常以IPXX作為等級區分,. IP為International Protection 的縮寫,國際上均以此做為保護等級辨識,. 第一個X所代表的意義 ... 於 kennyradio.pixnet.net -
#20.IPXX防水等級及防水測試方法 - ALTEAM 一路走來歡沁有你
1、定義IPxx 防塵防水等級防護等級採用國際電子電機委員會(IEC)推薦的IP××等級標準,不同的安裝場所,等級是不一樣的。具體可參照下面的說明選定。 於 alteam168.pixnet.net -
#21.ip54:參照標準,定義,防塵等級,防水等級,測試方法,(1)IPx 1,(2 ...
IPX4 模擬淋雨環境:360°全方位淋雨! 0 IP是Ingress Protection的縮寫,IP等級是針對電氣設備外殼對異物侵入的防護等級,來源是國際 ... 於 www.newton.com.tw -
#22.IP65防塵防水等級測試檢測報告辦理注意事項 - 今天頭條
IP防護等級包括:IP22、IP33、IP44、IP54、IP55、IP65、IP66、IP67、IP68等以及廠家自定義測試條件。 於 twgreatdaily.com -
#23.防塵與防水,防護知多少? | URBANER奧本電剪
國際防護等級認證International Protec tion Marking,是一種測量裝置防塵及防水能力的國際標準,所有電器用品要取得IP 等級都必須經過認證和獨立測試 ... 於 www.urbaner.com.tw -
#24.防護等級(IP)測試–進水和防塵-EAG實驗室
防護等級(IP)測試–水和灰塵的進入 ... 您的產品設計的防水性能如何? ... IP5X, 防塵, 通過檢查對它進行測試,以確保任何進入的灰塵都不會干擾零件的功能。 於 eag.com -
#25.防水防塵等級 - 行動裝置超簡單
5, 防塵(無可構成損壞的堆積), 5, 可阻擋低壓水柱 ... 灰塵防護測試方式 ... 防潑水及防水能力中的IPX5 與IPX6 兩項必需與IPX1、IPX2、IPX3、IPX4、IPX7 與IPX8 分開 ... 於 mobileiseasy.wordpress.com -
#26.【IP等級對照表】防水防塵分類如何看?看懂是防潑水還是潛水?
3C 產品、什麼是IP 防塵防水等級、耳機電子產品防水能力實際防水效果. 2021-11-17 ... 防水等級, 可防護類型, 防護有效性, 測試細節. 0, –, 沒有任何防護效果, –. 於 wattbrother.com -
#27.測試報告
Test sphere 12.5mm 測試鋼球ASIA QTECH. TSP-2/0802. ✓. DUST TEST CHAMBER 防塵試驗. 機. PTL. P14.41/5050255. Drip Box 防水試驗機. (IPX1~IPX2). 於 www.chimay.com.tw -
#28.軍規可靠度| Acer 台灣
藉由對產品進行MIL-STD-810H 標準測試以及異物防護(防水防塵) 測試,您可確保您的產品能承受比日常在教室、倉庫或現場更嚴苛的環境。 MIL-STD-810G Certified ... 於 www.acer.com -
#29.iPhone 11 防水測試,比官方標示的深度多一倍也沒事,兩台都 ...
這次iPhone 12 系列的防水防塵規格雖然還是IP68,跟上一代iPhone 11 一樣,但可放置的深度卻提升不少,從原本的2 公尺30 分鐘,變成6 公尺30 分鐘, ... 於 www.kocpc.com.tw -
#30.IP67/IP68 代表什麼? 一次看懂《IP 防水防塵等級表》 - Yahoo ...
但要注意的是,防水防塵的完美狀態,是指未經過落摔之前的測試標準,若產品經過落摔後,因為機體結構改變而造成進水現象,則不列入討論範圍. 於 tw.news.yahoo.com -
#31.選購耳機時都會有的疑問》IP等級夠高就一定能在水中使用?
iPhone XR防濺、防水和防塵,並在受控實驗室條件下進行了測試,並根據IEC標準60529(最大深度為1米,最長30分鐘)達到IP67等級。防濺,防水和防塵不是永久 ... 於 www.earphoneman.com -
#32.服務- 防塵與防水測試 - 全國公證
IEC 60529的防塵與防水(Ingress Protection, IP)測試能確保產品可忍受潮溼與充滿灰塵的環境。 Intertek所出的獨立報告能充份證明客戶所宣稱的IP功能,使產品更具效力。 於 www.intertek-twn.com -
#33.一看就懂IP 防水防塵等級表 - SPILL
有時見到一些防水產品標示為IPX8 / IPX5,其實「X」即是等於0,證明該產品並沒有任何防塵功能。 除此之外,你會發現有些耳機或智能手機的防護等級會寫成 ... 於 www.spill.hk -
#34.可靠性防水防塵測試方法介紹 - 雪花新闻
可靠性测试:www.renzhengcn.cn 在日常生活中,电子电器类产品都有一定的防尘防水能力,防尘测试常用作检测电子电工产品在微尘环境中的防护能力。 於 www.xuehua.us -
#35.手機防水標準大公開如何正確防護不進水
《 SOGI 手機王》就以最簡單的方式為大家介紹IP 防塵防水. ... 所標榜的「防塵防水」是什麼樣的測試標準,規格表上寫的IP68 防塵防水又適用於哪些情況, ... 於 www.sogi.com.tw -
#36.IP防護等級測試 - 暘致科技股份有限公司
IP測試簡介. IP是Ingress Protection的縮寫,IP等級是針對電氣設備外殼對異物侵入的防護等級,提供了一個以電器設備和包裝的防塵、防水和防碰撞程度來對產品進行分類的 ... 於 www.sunreach.com -
#37.防水防塵測試 - Thednc
防水防塵測試 簡介一般戶外電器產品(含成品與零組件),如防盜監視器、戶外燈具、交通號誌、水中電器、船用電器等。 依據標準:IEC 60529, IEC 60598, ... 於 www.thedncba.co -
#38.防塵防水IP Code 測試
針對產品的防塵與防水測試要求,依據測試規範IEC/EN 60529。只要是產品有需要防止固態物(solid objects),如手臂、手指、金屬棒、金屬線,甚至是粉塵或是液體(水) ... 於 hk.waltek.com.cn -
#39.SGS防塵防水IP防護等級測試服務 - Wfklee
IP測試請見如下: 防塵測試:IP1X~IP6X 防水測試:IPX1~IPX8 測試標準:GB/T 4208-2017 IEC 60529:2013/Cor.2:2015 ISO 20653:2013 詳細請聯系黃小姐,Tel:0755-2532 ... 於 www.aesntl.co -
#40.防水防尘等级及测试方式简介概要 - 百度文库
防水 防尘等级及测试方式介绍Consy.meng 2012.09.13 MITAC CONFIDENTIAL 目錄一、適用範圍及目的二、防水防塵等级介绍三、防塵測試方式介紹四、防水測試方式介紹2 一、 ... 於 wenku.baidu.com -
#41.常見問題-防水係數介紹 - GOSHOP知識庫
IPXX的第一個X 是防塵等級,第二個X 是防水等級 ... IPX2, 防滴型(II), 提供相同於IPX1 的防水保護,但又通過可向上15 度的四個定點防水測試。 於 help.goshop.com.tw -
#42.IP防護等級測試
IP 是Ingress Protection(進入防護)的縮寫。 IP等防護級系統提供了一個以電器設備和包裝的防塵、防水和防碰撞程度來對產品進行分類的 ... 於 www.origo-certification.tw -
#43.IP67/68防水測試報告-豐悅國際科技有限公司
*豐悅國際科技歡迎您~ i-life 防水透氣PTFE 奈米薄膜_防水/防塵/防油汙膜另有防PM2.5口罩販售* ; 防水透氣膜(IP67/68等級) PTFE Membrane ... 於 www.fji.com.tw -
#44.IP66,IP67,IP68代表什麼? 教你看懂防水防塵-國際防護等級認證
對照上方的表可以得知IP67的機器防塵已達完全防塵,防水部分也達到可以泡水30分鐘. 但是要注意的是通過測試的防水機可防水但不防肥皂水、海水,因為特殊液體可能造成 ... 於 www.gabil.com.tw -
#45.3-2-4 電器外殼防塵防水(IP) 試驗服務
本中心數十年來已成為國內電器業者最主要的檢測夥伴,並榮獲各縣市政府驗收案件之指定實驗室,可謂防塵防水試驗公信力之代名詞。服務產品各類電器產品(適用於額定 ... 於 www.tertec.org.tw -
#46.一張圖看懂外接儲存裝置的防護等級 - 威剛科技
越來越多電子產品標榜著防塵防水的功能,且都標示著IP68, IP57, IPX7, IP5X 等數值, ... 從圖中標示的等級,分別用滴、濺、噴射、浸泡的方式進行測試認證。 於 corp.adata.com -
#47.「防水防塵測試」懶人包資訊整理 (1) | 蘋果健康咬一口
測試範圍, 試驗設備符合. 任何要求防塵防水IP等級之產品 ... ,201202062026防水防塵試驗?知識專輯. 防水防塵測試、IEC 60529、CNS 14165、防盜監視器、戶外燈具、交通號誌 ... 於 1applehealth.com -
#48.NEMA 250 and IP Rating 防水防塵測試認證 - Eurofins E&E ...
NEMA 250 and IP Rating 防水防塵測試認證. 電器製造商協會(National Electrical Manufacturers Association,簡稱NEMA)一家位於美國華盛頓的技術標準機構,雖然有 ... 於 metlabs.tw -
#49.看Nikon 如何測試D850 的防水防塵能力,做出一部「沒有一 ...
Nikon 在去年8 月推出的單反 D850 除了以4,575 萬像素背照式CMOS、 EXPEED 5 影像處理器、9 FPS 連拍速度等攝影規格為主打外,機身的防水防塵能力也是 ... 於 photoblog.hk -
#50.IP66防塵防水測試哪裡可以做? - MP頭條
IP66防塵防水測試常用於測試燈具、航空插頭、防水插座盒,電話手錶等電氣產品外殼的IP防護等級,東莞北測標準技術服務是具備CNAS和CMA資質的第三方IP ... 於 min.news -
#51.什麼是IP68等級?一次搞懂防塵防水等級意義 - 殼老爹官網
所謂的IP 等級,簡單來說是指產品的「防水等級」、「防塵等級」, IP 英文 ... 新產品後,會將產品送去檢測機構進行測試,為的就是要取得防塵防水等級 ... 於 www.cloudshop.com.tw -
#52.京灣檢驗科技股份有限公司
外殼防塵、防水IP 等級測試報告. 委試公司:華能光電科技股份有限公司. 委試公司地址:新北市新店區中正路542-4號6樓. 產品名稱:防水型LED燈. 型號/商標:TA20CH84D2AB1. 於 www.energyled.com.tw -
#53.IEC 60529 外殼保護等級| 電子電器產業 - SGS
建議測試之產品(適用額定電壓小於72.5KV之產品): ... 若產品標準沒有特別規定,IPX1 ~ IPX9 防水試驗的要求為:. 不得影響產品的正常操作; 不得為害產品的安全 ... 於 www.sgs.com.tw -
#54.iPhone 真的能夠防水嗎? IP68與IP67兩者差別是什麼? - 瘋先生
iPhone XS 與iPhone XS Max 皆具備防潑抗水與防塵功能,並且已在受控管的實驗室環境條件下測試,達到IEC 60529 標準的IP68 等級(在最深2 公尺水中最長 ... 於 mrmad.com.tw -
#55.水深十米殘酷測試!iPhone 7 防水力完勝三星Galaxy S7?
iPhone 7 以及iPhone 7 Plus 的防水防塵等級為IP67,因此照理來說可以在1 公尺內的淡水下撐上30 分鐘;三星的Galaxy S7/S7 Edge 採用的則是IP68 防水 ... 於 3c.ltn.com.tw -
#56.[新聞] 80%人都理解錯了防塵防水等級知識詳解
不過這裡需要注意的是,防水測試的標準與定義,都是在"靜止"的“清水”中所 ... 千萬別以為你的耳機、手機具備IP68防塵防水,就可以拿到游泳池裡使用或 ... 於 www.ptt.cc -
#57.IP等級測試 - 中文百科知識
(1)IPx (7)IPx (8)IPx防水防塵(IP防護等級)定義: IP等級系統提供了一個以電器設備和包裝的防塵、防水和防碰撞程度來對產品進行分類的方法,這套系統得到了 ... 於 www.easyatm.com.tw -
#58.防水防塵試驗@ 昌盛光電Prosper OptoElectronic Co - 隨意窩
防水防塵測試 、IEC 60529、CNS 14165、防盜監視器、戶外燈具、交通號誌、水中電器、船用 ... 於 blog.xuite.net -
#59.Pro'sKit 寶工MT-8100 防水型電話測試器
商品介紹. 通過IEC/EN60529 國際外殼機構保護等級IP 54 防水、防塵測試。 具拋落保護的堅固外殼。 通過CE安規認證。 高阻抗監聽電路。 外線電壓測試; 電話線通斷檢測 於 shop.prokits.com.tw -
#60.什麼是IP68 防塵/防水等級呢?與IP67、IP57、IPx7 這些標示又 ...
國際防護等級認證International Protection Marking (IEC 60529)規範定義的防塵防水等級,都是指的是在「靜止的清水」環境之中進行測試的結果! DSC06634 ... 於 ifans.pixnet.net -
#61.【認證】錄安鏡頭通過IP68防塵防水測試報告- 最新消息
【認證】錄安鏡頭通過IP68防塵防水測試報告. 回上頁. 0則留言. 排序依據. 最新, 最舊. Facebook 留言外掛程式. 錄安科技有限公司 公司:(02)2910-5727 於 www.luan168.com.tw -
#62.防水防塵測試的標準是什麼 - Haowai.Today
防水測試防塵測試防塵測試 用於檢測電工電子產品、汽車摩托車零部件、密封件在砂塵環境中防止砂塵進入密封件和外殼的試驗,確定空…… 於 www.haowai.today -
#63.公司簡介 - 鐵木真科技股份有限公司
開始研發防塵、防水性能測試設備,並於同年8月順利取得全台灣最大車燈製造廠大億交通公司訂單。 1986年. 成立鐵木真電機有限公司,專業生產鹽水噴霧試驗機,年產約120 ... 於 www.t-machine.com.tw -
#64.防水防塵測試設備 - 阿里巴巴商務搜索
阿里巴巴為您找到76條防水防塵測試設備產品的詳細參數,實時報價,價格行情,優質批發/供應等信息。您還可以找ip防水測試設備,ipx7防水測試設備,ipx5防水測試設備,ip65 ... 於 tw.1688.com -
#65.設備介紹 - 京鴻檢驗科技股份有限公司-
測試 產品對於風雨水漬之耐水性、防水性之試驗(IP防水試驗)。 防(耐)塵試驗機. 測試產品對塵埃的防塵性之耐久度(IP防塵試驗)。 於 www.jhet.com.tw -
#66.[新聞] 80%人都理解錯了防塵防水等級知識詳解- mobilecomm
不過這裡需要注意的是,防水測試的標準與定義,都是在"靜止"的“清水”中所 ... 千萬別以為你的耳機、手機具備IP68防塵防水,就可以拿到游泳池裡使用或 ... 於 pttdigit.com -
#67.UL 實驗室參訪!替你的3C 家電產品安全把關
UL 是獨立的第三方安全認證單位,以嚴謹的測試確保產品的安全性。本次透過參訪UL 在台灣的測試實驗室,實際觀看材料測試、IP 防水防塵等級測試、USB ... 於 lawrencehou.blogspot.com -
#68.IP防塵防水測試怎麼做? - 多源焦點
什麼是IP防塵防水測試? 如今,消費電子產品標有防塵防水的標籤很常見,這通常是通過IP等級標準完成的,其中包括IP68、IP57、IPX7、IP5X 等等級。 於 dyfocus.com -
#69.你的手機真的防水嗎?下雨天、海邊玩水記得幫手機穿上雨衣
而IPXX,第一碼為「防塵係數」,第二碼為「防水係數」,每個級別皆有不同測試。 我們常看到主打防水的手機,常見的防塵防水係數為IP65、IP67、IP68。 IP65 ... 於 www.bonecollection.com -
#70.防塵試驗設備 - 益安信科技
防塵 試驗箱. 型號: P03.17. 砂塵試驗箱是根據IEC60598-1《燈具一般安全要求與試驗》、IEC60529《外殼防護等級(IP 代碼)》標準要求設計製造,用於IP5X/IP6X 耐塵測試 ... 於 www.emctech.com.tw -
#71.防水防塵測試-PTT/DCARD討論與高評價網拍商品-2021年11月
防水防塵測試 在-PTT/DCARD討論與高評價商品,提供洗衣機防水防塵套、SONY防水防塵手機、手機殼防水防塵在露天、蝦皮優惠價格,找防水防塵測試相關商品就來飛比. 於 feebee.com.tw -
#72.燈具安全通則試驗報告(防塵防水) - 昶旭能源
燈具安全通則試驗報告. (防塵防水). 測試標準: CNS 14335 C4480(88 年版). 收件日期: 106 年01 月20 日. 測試日期: 106 年02 月13 日至106 年02 月14 日. 於 www.cooled.com.tw -
#73.防水防塵測試– Budzak
防水防塵測試 簡介一般戶外電器產品(含成品與零組件),如防盜監視器、戶外燈具、交通號志、水中電器、船用電器等。 依據標準:IEC 60529, IEC 60598, CNS 14165, ... 於 www.budzak.me -
#74.教你看懂防水防塵IP代碼-國際防護等級認證 - 我的智慧家庭
深度由製造商指定,市面上標榜防水等級IPX8智慧型手機測試深度通常為2m。 ... 透過以上防水與防塵數字的說明後,可以了解一支宣稱IP67的手機代表著它 ... 於 myfone.blog -
#75.IP防護等級測試 - 溫度記錄器/ 數位電表/ 校正儀器
用於檢測設備防水進入的程度,以驗證其保護等級第二數字碼為1的”防滴水”及2的”在 ... 與IP6X”塵密(完全密封防塵)”保護等級,符合IEC 60529標準2001-02§13.1表VII圖2. 於 www.qtech-instrument.com.tw -
#76.國際防護等級認證- 維基百科,自由的百科全書
有時候也被叫做「防水等級」「防塵等級」等,定義了機械和電子設備能提供針對固態 ... 部份測試是獨立的,數字高的測試並不一定能取代數字低的測試,例如標稱IPX7的 ... 於 zh.wikipedia.org -
#77.IP65防護等級檢測報告辦理詳細流程 - 日間新聞
IP6X表示防塵試驗,要求完全防止粉塵進入;. IPX5表示防噴水試驗,要求產品在各表面噴水,產品無水滴進入。 IP65防水防塵測試依據標準. IEC標準 ... 於 www.daytime.cool -
#78.偷窺UL台灣實驗室#IP防水防塵等級測試「越來越多手機
偷窺UL台灣實驗室#IP防水防塵等級測試「越來越多手機、相機等3C 器材加入防水防塵功能,也有許多大型家電因需長時間暴露在潮溼或雨淋等戶外環境,而需要加入防水規格。 於 www.facebook.com -
#79.【手機專知】什麼是防水防塵等級?IP XX數值的意義?
防塵防水 的手機是否需要手機保險. 由於異物防護等級的測試都是在環境可控的獨立實驗室中進行,因此在自然 ... 於 www.jyes.com.tw -
#80.防水防塵測試
依據標準:IEC 60529, IEC 60598, CNS 14165, EIA-364, P1。 防水試驗. IPX1, 放置樣品之旋轉台其旋轉速率為1轉/分,水流率 ... 於 www.etc.org.tw -
#81.環境可靠度測試 - 翔吉科技
測試 項目有防水:IPX1~IPX8;防塵:IP1X~IP6X。 IPX3:對垂直線兩側各60度來回擺動,測試時間定為 ... 於 www.cal-tech.com.tw -
#82.防水防塵測試費用的蘋果、安卓和微軟相關APP,DCARD
防水防塵測試 費用的蘋果、安卓和微軟相關APP,在DCARD、PTT.CC、FACEBOOK、MOBILE01和這樣回答,找防水防塵測試費用在在DCARD、PTT.CC、FACEBOOK、MOBILE01就來APP軟體 ... 於 app.mediatagtw.com -
#83.防水防塵(IP) - 服務- 產業
防水防塵 (IP). 防水防塵(IP). IP代碼(IP Code)是一種編碼系統,用於指示外殼提供 ... 針對各類型的產品外殼,我們提供下列產品標準測試服務:. IEC 60529 IP42 測試。 於 www.victronic.com.tw -
#84.IP防護等級防塵防水測試有哪些方法? - 壹讀
IP代碼第一位特徵數字是代表防塵等級,第二位特徵數字代表防水等級。在國際上有一專門的測試規範IEC/EN60529.排名靠前標記數字表示接觸保護和外來物保護 ... 於 read01.com -
#85.IP防水防塵測試設備_產品中心 - 得邁斯儀器股份有限公司
PWB IST互聯應力測試系統 · Introbotix 信號損失量測系統 · Introbotix 特性阻抗量測系統 · Introbotix 背鑽深度量測系統 · Keysight 網路分析儀 · Tektronix 時域反射儀 ... 於 www.qtechinstrument.com -
#86.這款相機的防水、防塵及防震性能如何? | Sony TW
防震性能: 符合MIL-STD 810F Method (測試方法) 516.5-Shock (衝擊) 標準。 本產品已通過從5 公分厚膠合板上方1.5 公尺高度掉落的測試。 測試條件:關閉液晶面板,液晶 ... 於 www.sony.com.tw -
#87.財團法人車輛研究測試中心- 實驗室瀏覽 - 經濟部標準檢驗局
類別, 產品測試- 防水防塵測試. 實驗室名稱, 財團法人車輛研究測試中心. 實驗室地址, 50544 彰化縣鹿港鎮彰濱工業區鹿工南七路六號. 網址, http://www.artc.org.tw. 於 www.bsmi.gov.tw -
#88.IP67/IP68 是什麼?手機防水防塵等級說明
例如Apple 官網是這麼說的:. iPhone X 具備防潑抗水與防塵功能,並且已在受控管的實驗室環境條件下測試,達到IEC 60529 標準 ... 於 www.chineseineurope.com -
#89.防水防塵實驗室 - 金屬中心檢測驗證網
防塵防水 IP等級:. IP等級可分防塵、防水兩部分,其中防塵共分0~6 七個等級,防水共分0~8 九個等級. 測試範圍, 測試項目. 任何要求防塵防水IP等級之產品 ... 於 www.quality.org.tw -
#90.IP55防護等級測試_外殼防塵防水等級第三方CNAS檢測機構
此處已新增小程式,請到今日頭條客戶端檢視)IP防護等級測試能力本中心配備了淋雨實驗室,不鏽鋼材料的垂直淋雨、擺管淋雨、防噴、防濺、水浸等防水 ... 於 www.gushiciku.cn -
#91.什麼是IP65、IP68? 防水防塵? 國際防護等級怎麼看?
IP防水防塵等級國際防護等級Ingress Protection Rating IP代碼| 沛禮國際 ... 通過測試的防水產品雖然可以防水,但不能防肥皂水、清潔劑及海水等, 於 www.polit.com.tw -
#92.說明指南| 本Walkman的防水與防塵效能 - Sony Corporation
使用前,請務必閱讀並充分瞭解防水/防塵規格。 (*1) 耳機部分不完全防水。 (*2) IPX5 (防水流的保護等級):Walkman在裝上游泳耳塞時,經過測試可在下列測試條件 ... 於 helpguide.sony.net -
#93.暐誠國際驗證股份有限公司
大型防水測試機. 雨淋/噴濺/沉浸試驗. 廠牌: 鐵木真; IEC 60529 IPX1 / IPX2 / IPX3 / IPX4 / IPX5 / IPX6 / IPX4K / IPX6K / IPX9K; IPX3 ~ IPX4: R400 mm 、R800 mm ... 於 atcreliability.com -
#94.防水試驗(IPX4、IPX5、IPX6) - 東方馬達
防水 試驗(IPX4、IPX5、IPX6),透過影片,您可以看到在每種測試條件下如何排水. ... 製品情報. ・ BLE2系列-200W輸出機型備有防塵、 防水規格IP67 連接器型 ... 於 www.orientalmotor.com.tw -
#95.IP6X和IPX4即為IP64,標準中對這兩項的定義為: 防塵等級IP6X ...
例:有秤或顯示儀表標示為IP65,表示產品可以完全防止粉塵進入及可用水沖洗無任何傷害。 IPxx等級中關于防水實驗的規定。 (1)IPx 1. 方法名稱:垂直滴水試驗 ... 於 www.itsfun.com.tw -
#96.IP69(IP69K)測試報告的測試定義說明
IP68 防水防塵等級已不夠,IP69(IP69K)最高防水防塵等級的定義. 是什麼? IP 等級乃是一種國際防護等級認證(International Protection Marking,IEC. 60529),也稱作異物 ... 於 io-power.com.cn -
#97.防塵防水測試丨防塵防水等級標準及測試方法 - 每日頭條
試驗時間為3min;IPX7:短時間浸水,浸入規定壓力的水中經規定的時間後外殼浸水量不至於達到有害程度,放置於一個潛水箱中,一般深度1米, ... 於 kknews.cc -
#98.IP等級防水防塵異物防護等級 - 雷伯斯儀器
測試 時間:持續浸入水中至少1小時。 深度由製造商指定,市面上標榜防水等級IPX8智慧型手機測試深度通常為2m。 9K, 高溫高壓水柱 ... 於 rebers.com.tw